Global Supply Chains and Labor Rights: Any Reasons for Optimism?
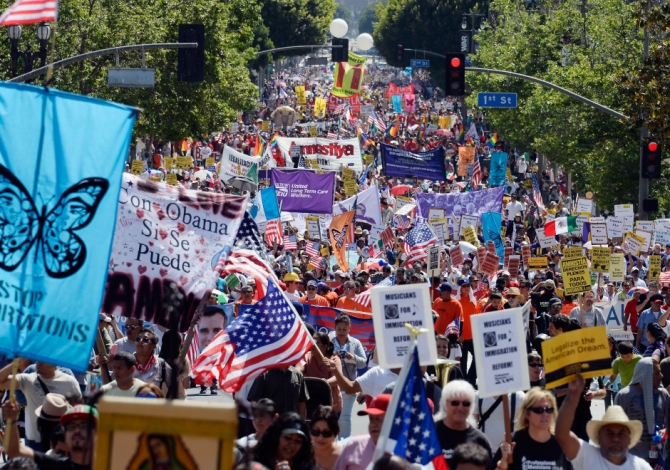
The recent May Day marches drew attention to the challenges and opportunities presented by the contemporary global economy. In many instances, trade and financial openness have facilitated growth, employment, and lower prices for consumers. But trade competition can dislocate workers, sometimes persistently. And while extreme poverty has been reduced worldwide, its reduction has been uneven geographically, and economic growth often has been accompanied by increased income inequality.
In many locations, workers also confront hazardous employment conditions. Last week marked the fourth anniversary of the Rana Plaza disaster, in which the collapse of an eight-story building in Savar, an industrial suburb of Dhaka, resulted in the 1,129 deaths and 2,500 injuries. Rana Plaza was designed as an office building, but several garment factories operated on its upper floors. These factories produced for a range of global brands, including Benetton, Bon Marche, The Children’s Place and Primark. Although the factory owners were aware of structural cracks in the building, they nonetheless insisted that their workers enter the building on the day of the collapse.
Rana Plaza attracted global attention, but it was only one – albeit the deadliest one – in a series of industrial accidents involving the Bangladesh ready-made garment sector. Activists hoped that, like the 1911 Triangle Shirtwaist factory fire in New York, Rana Plaza might lead to improvements in worker safety in the apparel sector.
Such improvements are difficult to achieve, given the competitive pressures of the global garment industry. With the end of the Multifibre Arrangement (1974-2004), which had set country quotas for apparel and textile exports to developed nations, the competition among developing country producers became especially fierce. Lead firms – retailers and brands, many with global reach – rarely retain direct ownership of their production facilities. Rather, they rely on arms-length, market based transaction to source inputs, cut and sew fabric and complete final assembly. Nike, for instance, employs 62,000 workers directly, mostly in the US and Europe. But approximately 1 million workers are employed in its subcontractor facilities. Each of an apparel firm’s production stages may employ multiple subcontractors; and subcontractor firms also may diversify, producing for multiple brands and buyers.
In apparel, subcontracts typically reward cost and speed: production activities typically are labor-, rather than skill- or capital-intensive. Brands and retailers sell to consumers who have come to expect relatively low-cost, frequently-changing clothing. Producing cheaply and quickly are therefore key to winning subcontracts; but this also suggests paying workers low wages, asking them to work long hours, and investing little in worker safety. And when global demand for apparel falls, as it typically does during economic downturns, these pressures become even more pronounced, making industrial accidents more likely.
But, with the passing of another year of May Day marches, perhaps there is some room for optimism. Under some conditions, participation in global supply chains could be a mechanism for improving – or at least, for not harming – worker rights. Indeed, long-standing economic models suggest that, given their relative abundance in low- and middle-income countries, less-skilled workers should benefit from trade and multinational production. Specializing in labor-intensive goods and exporting those goods elsewhere allows workers to capture gains that would otherwise be unavailable (although see this recent piece for a contrary finding). In this sense, factory jobs may well be preferable to employment in the rural and/or informal sector. Such jobs also may offer women access to opportunities and independence that are otherwise unavailable.
In my research, I find that the positive benefits to workers of multinational production are more likely to accrue under certain conditions. First, when multinationals directly own production facilities, rather than subcontracting production, worker rights tend to be better-respected. Direct ownership is more likely in capital- and knowledge-intensive activities, though, suggesting that this route to improvements may have little impact in countries such as Bangladesh.
Second, when developing countries export their products to countries with strong labor rights protections, their labor rights environment is likely to improve over time. This “trade-based” diffusion of labor rights occurs because firms, shareholders, and/or consumers in export destinations care about the conditions under which their goods are produced. Trade also can serve as a mechanism for rights improvements when labor conditions are included in (and enforced as part of) preferential trade agreements; and when destination markets with substantial buying power impose reporting or other requirements on producers (e.g. the state of California’s Transparency in Supply Chains Act). Of course, such processes require that consumers, activists, and lead firms have sufficient information about where, and under what working conditions, their goods are manufactured. In a world of supply chain production, access to such information is by no means automatic. Groups such as Human Rights Watch are, however, pressuring large firms to provide such details, and naming those that refuse to participate.
Third, firms in developing countries may perceive that improvements in their labor standards will allow them to gain access to global supply chains. Because participation in global production can allow firms to expand production and sales, and perhaps to benefit from the diffusion of new production and management technologies, they may benefit materially from labor-related improvements.
To test this potential mechanism, Edmund Malesky and I recently surveyed foreign-owned firms in Vietnam about their willingness to make labor-related improvements. These firms are typically small, employing 125 workers on average, and most are owned by firms elsewhere in Asia (Japan, South Korea, Taiwan and China are the most common). These firms, which participated in the broader Provincial Competitiveness Index survey, were asked to imagine this scenario:
“You’ve been contacted by an international consulting company, which works to connect large multinational firms to suppliers in emerging markets. This consulting firm wants to shortlist your company, along with two other firms in your region, as potential suppliers to a European/Indian company that sells primarily to the European/Indian market. To be eligible for the shortlist, the consulting company requires that your firm adopt the multinational’s Labor Code of Conduct for Suppliers. This Code of Conduct includes greater representation for workers, limits on overtime work, and regulations to protect the health and safety of workers. Adopting the Code of Conduct will allow you the possibility of future orders from this multinational and others like it, but it also will increase your operating costs.”
We then asked respondent firms how much, as a percentage of their current operating costs, they’d be willing to spend to make such improvements. Our “contingent valuation” question also had an experimental component: some firms were asked the question with the multinational and consumer market described as “European.” Other firms were asked the same question, but the multinational partner and market was “Indian.” By randomly varying this element, we sought to understand how incentives for labor rights improvement might vary with destination market (and with opportunities for higher product markups).
Our findings were somewhat encouraging: on average, firms were willing to spend 6.5 percent of their operating costs to make such improvements. And we find that firms that received the “Europe” version were willing to spend more (about half a percent, a statistically and substantively significant amount) than those with the “Indian” version. One could imagine that these effects also vary across industries: indeed, the Europe-Indian difference was much greater for the firms in our survey that produce apparel, compared with those that produce plastic carrier bags. The former operate in an industry in which much attention has been paid to worker rights, and in which the difference in markups between the European and Indian market can be substantial. Activists have paid little attention to the latter – of which there are a significant number in Vietnam’s foreign-invested sector – and demand for their product has fallen in Europe, as many governments have moved to outlaw or tax plastic bags. Indeed, Vietnamese firms in the plastics sector reported being willing to invest more in labor-related improvements when India, rather than Europe, was named as the destination market.
Our analyses also indicate that we have much more to learn about how global supply chain involvement might be consistent with improvements to labor rights. Such a process likely requires sustained attention from lead firms, shareholders, consumers, activists, intergovernmental institutions, or some combination of these. And researchers continue to face challenges, given firms’ unwillingness to share information on the structure of their supply chains, in studying these dynamics systematically.
Finally, capturing gains from multinational production is not simply an economic process. It is also a political one: if workers do not have the rights to form unions or to bargain collectively, then it may be factory owners and other elites who capture the bulk of the benefits from multinational production. At the country level, having a democratic political system and a left-leaning government make labor rights protections significantly more likely. Competent and unbiased labor inspectors also can work, independently or with non-governmental organizations and private associations, to implement labor regulations. And private sector initiatives that encourage workers to report occupational health and safety concerns (like the Bangladesh Accord on Building and Fire Safety) depend on workers having voice vis-à-vis their employers. Such voice depends on governments providing and enforcing legal protections. Not surprisingly, then, analyses of private-sector based efforts to govern labor rights typically find that these work best as a complement to, rather than a substitute for, public sector governance of rights.